Material Requirement Planning (MRP) remains at the heart of any enterprise planning process, for it calculates the amount of input materials and components needed to manufacture a product. However, it is definitely not as simple as it means.
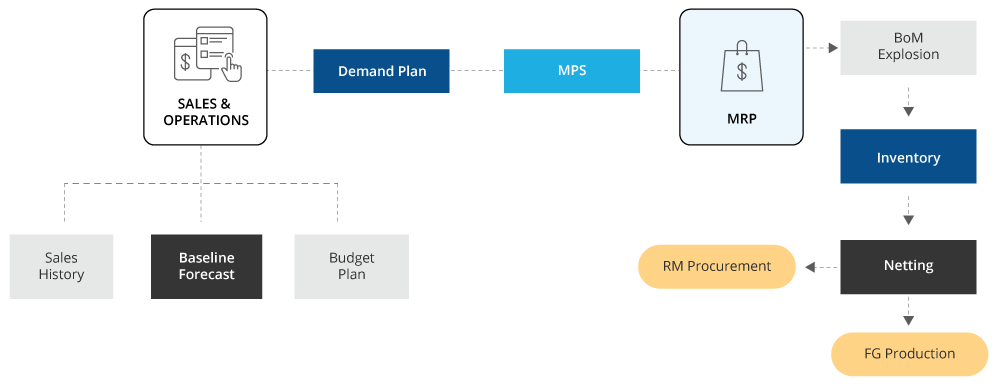
The reason is that MRP is not a standalone process – and has dependencies on Demand Forecast, Master Production Schedule, Raw Material Inventory status, Open Purchases from Vendor and Finished Goods Inventory and more. As it is connected with various systems, stakeholders or data points, it becomes one of the most focused tasks within an organization.
Every MRP process has two basic goals i.e. Procurement & Production.
It is obvious that Procurement Planning is triggered by Material Requirement Planning as it helps answer the question “What & how much must we buy to make the end-product?”. This also must take in to account an enterprise’s current stock of Raw Materials which was procured in the past. Based on these inputs, the Production Plan helps the enterprise determine “How much Finished Goods need to be produced?”.
Material Requirement Planning KPIs
The effectiveness of Material Requirement Planning in achieving the above two goals is determined by two important KPIs / objectives.
1. Low Inventory Levels: Working Capital remains a sensitive part of an enterprise and it is vital to optimize its Capital Management system. Significant amount of responsibility is passed on to Manufacturing & Operations units to keep the inventory levels low. Hence, a successful and responsible MRP process also considers how much they can buy from vendors and how much they can store.
2. On-Time Production: Procurement and Sourcing teams are mainly dependent on MRP process in order to execute their respective tasks. Similarly, Production Teams also rely on MRP outputs to ensure they know what to produce. Relatively, it is the responsibility of Buyers to get the required materials from Vendors on time and likewise the Production Team must ensure that the goods will get produced on schedule with the available material. No doubt, this is one of the important performance matrix for an Operations Department.
In our next blog, let us discuss some of the determinants and drivers of a good Material Requirement Planning process.
To learn how ValQ can be used to drive effective Material Requirement Planning for mid- and large enterprises, reach out to us today.
Or you can also try out a free trial of ValQ today .